3 Warehouse Types for E-Commerce Distribution
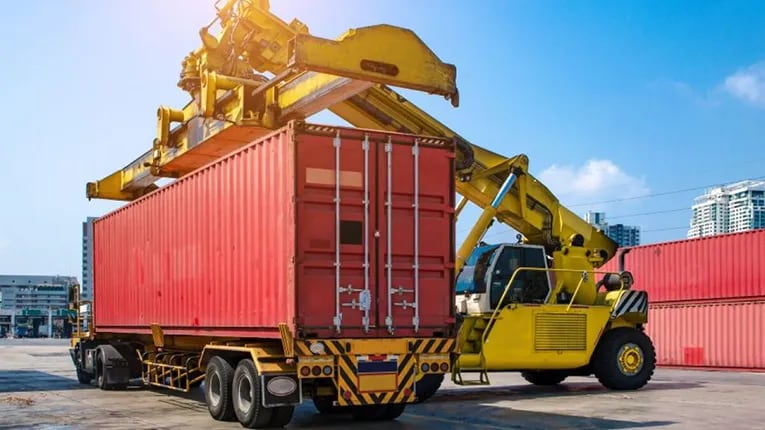
Let's face it: nomenclature around warehouse facilities can be confusing. Is it an industrial property, a warehouse, a fulfillment center, a distribution building or something else? Further complicating the issue is that the response to that question can often be "all of the above," leaving the inquirer even more perplexed.
To begin to sort this out, LoopNet spoke with two real estate professionals that concentrate on industrial product types: John Dettleff, a commercial real estate broker and senior managing director at JLL, who is focused on the leasing and sale of industrial properties in the Washington, D.C., metro area, and Kate Nolan Bryden, a senior vice president with MRP Industrial, a development firm based in Baltimore, Maryland that builds and manages institutional-grade industrial properties.
To bring some focus to the broad area of industrial real estate, Dettleff suggested focusing on the warehouse/distribution segment relating to e-commerce, which is the portion of the industrial market that has experienced the most development and leasing activity over the past decade and continues to be a focus for both real estate owners and industrial users.
For e-commerce companies and traditional retailers with robust e-commerce platforms, the distribution chain varies based on the items they sell and the customers they serve. But overall, the chain includes three types of warehouses, each of which is situated in a strategic location and carries out a somewhat distinct activity.
The three primary warehouses involved in e-commerce distribution are:
- Break-bulk facilities at the national level.
- Fulfillment centers in regional locations.
- Last mile warehouses in urban and suburban infill areas.
National, Regional and Local Warehouses
Dettleff said that a good way to delineate the type of facility required in a particular location is to ask, "are you building [for] the national, the regional or the last mile [user]?"
Always careful to qualify his statements, Dettleff said that generally, at the national level when items arrive at a port, they go to a break-bulk facility where massive quantities are broken down into smaller clusters for transport to regional locations. At the regional level, items can either be stored or sent directly to consumers. In major metropolitan areas, items stored in regional warehouses are typically sent to last mile facilities, which are located close to consumer homes, enabling fast delivery to customers.
Asked about the sizes of each of these facilities, Dettleff said it's hard to generalize because each vendor's supply chain is different, "but you essentially have million-square-foot warehouses [nationally], 400,000-square-foot warehouses [regionally], and then, 50,000- to 100,000-square-foot [structures for] last mile delivery."
Bryden noted that, "technically, they are all warehouses, with cross-docking capabilities."
The New Warehouse Distribution Network
"E-commerce is greatly changing the way that this whole [warehouse distribution] sector is working," Dettleff said. Using a pair of shoes as an example, he said that in the past a box full of shoes would be taken to a store from a warehouse roughly once a week. "You just needed to get there once a week, not every day, so you could put your retail warehouses far away." But today, warehouses that pick items from shelves and package them for individual delivery in order to fulfill online orders are dubbed fulfillment centers. They are situated closer to consumers so individual items can be delivered quickly to people's doorsteps.
Dettleff said that the traditional retail distribution model of warehouse to store is obsolete if you carry out direct-to-consumer, e-commerce or omni-channel retailing, terms that he says are all interchangeable. "If you want an e-commerce business, you have to start an entirely new warehouse distribution network. I mean, you literally have to start from scratch," he noted.
To build out this chain, Dettleff said retailers need different types of warehouses in a variety of locations and the first question they need to ask is "where does my product come in?"
"Most [finished consumer goods from Asia] come in through the port of L.A. and then they go somewhere [else] in the country like Chicago or Dallas," said Dettleff. But Bryden noted that apart from finished goods from Asia, all types of items enter U.S. ports ranging from fish, meat and coffee to minerals, pharmaceuticals and building products.
Break-bulk Warehouses
Uses. These warehouse structures tend to serve as initial transfer points for goods that arrive in massive quantities, either in sea containers or as "break bulk." This is a shipping term for cargo that does not fit in a standard shipping container and is instead transported individually in crates, bags, barrels, etc. The term is also used as shorthand to describe the warehouses in which contents are broken down, regrouped and transported to regional locations.
Locations. These facilities are generally located in or near the largest industrial markets and seaports across the U.S., such as Long Beach, California, Dallas, Chicago and Newark, New Jersey. These are often massive industrial sites with hundreds of warehouses close to major multi-modal transportation hubs that can include shipping lines, rail lines and extensive highway networks.
Bryden said that "land directly proximate to these ports is often gobbled up by commodity storage," and this makes "that land much more valuable to the port for that use, so these bulk facilities can be an hour to 90 minutes away from the port and still be completely functional for the tenants."
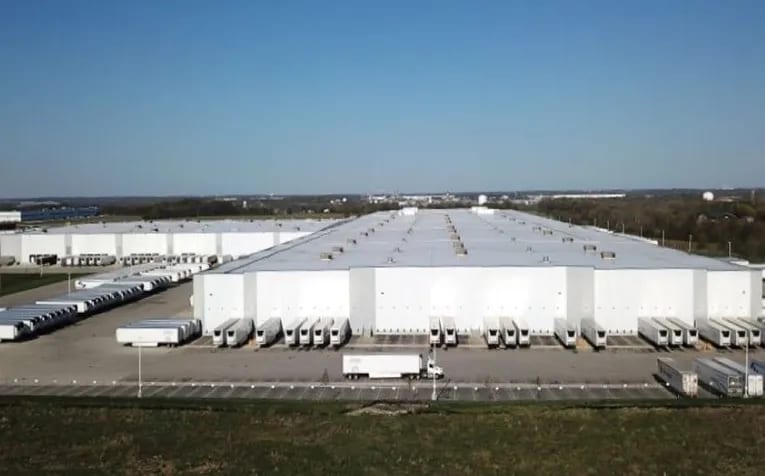
Design and circulation. The buildings, according to Bryden, are largely designed as cross-dock facilities. This means that tractor trailers park at loading docks on one side of the facility and their contents are unloaded, sorted and reloaded onto trucks parked on the other side of the building, ready to depart as soon as they are loaded.
"The bulk facilities usually range in size from 500,000 square feet to more than 1.5 million square feet. They're typically set up with cross-dock capabilities, though tenants may not utilize them in that way or they may use just a portion of the building for cross-dock activities," Bryden noted. "Operations are highly individualized from tenant to tenant," she qualified.
In the e-commerce age, building clear heights have become a critical dimension in warehouse design. Clear height is space that is unimpeded by building features such as joists, lights or sprinklers, which enables users to operate tall pieces of equipment or conveyor systems with vertical components without obstruction. "What we've been seeing is that 36- to 40-foot-clear is the standard, though not all tenants require this," so some users may be in buildings with clear heights of 40 feet but they will not utilize the entire cube because of the commodity or storage method in question, Bryden said.
Bryden emphasized the importance of circulation, parking and storage for tractor trailers. "We're seeing greater demand for trailer storage than what was typical five to 10 years ago," Bryden said. She noted that for bulk facilities, one trailer space per 5,000 square feet of building is ideal.
Demand for employee parking has also increased in recent years. "While it's true that technology and conveying systems are used in bulk facilities to optimize through-put, we've still seen significant demand for labor among our tenants and ensuring these buildings are set up to support their workforce is critical," Bryden noted. Though at times more employee parking is requested, the target ratio for personnel parking is one car space per 2,000 square feet of building.
Regional Fulfillment
Uses. For e-commerce, regional facilities tend to be utilized in one of two ways. They can be used to store items that will eventually be sent to different warehouses before they are shipped to consumers, or they operate as fulfillment centers that send packages directly to purchasers.
"There is a diverse user base for mid-size buildings, ranging from middle-mile support for national users to regional or local businesses serving local customers," noted Bryden. "These facilities work well, too, for users who store very specialized goods like pharmaceutical supplies or components," she added. Additionally, food suppliers became even greater users of this type of warehouse during the pandemic.
Locations. These facilities tend to be located on the outskirts of major metro areas. In Washington, D.C., for example, Dettleff said that regional distribution centers are in places like Frederick, Maryland, the I-81 Corridor, Richmond, Virginia and Baltimore, Maryland. Bryden said that most finished goods are sent by trucks rather than rail so proximity to interstate highways is key.

Design and circulation. These buildings can range in size between 150,000 and 400,000 square feet according to Bryden and Dettleff, but each emphasized that these are just general ranges.
"Usually the building [clear heights] are somewhere between 28 and 36 [feet], but I would say most commonly, 32-foot-clear is considered optimum," Bryden said.
For parking, Bryden emphasized that "space for trailer parking and van parking is still a major part of the equation for mid-size buildings. The functionality of the site is just as important to most users as the functionality of the building itself, so this needs to be well understood by the developer." These spaces tend to be 60 feet and 30 feet long respectively, said Bryden. Personnel parking can be slightly greater proportionally in mid-size buildings than in bulk facilities with 1.5 parking spaces per 1,000 square feet of building considered optimum.
Dettleff emphasized that these properties require "incredible amounts of power" to charge forklifts and other vehicles, as well as air conditioning that is going into employee intensive facilities. "Typically, mid-size buildings are developed with 2,000 to 3,000 amps of power and that is often sufficient for a 150,000- to 400,000-square-foot building. However, refrigeration needs within a building can drive that to 4,000 amps and beyond," noted Bryden.
The Last Mile
Uses. For e-commerce, "you've got tractor trailers coming in from the regional level ... so every night ... they're filling up these facilities with either what the orders are or what they think the orders are going to be based on their algorithms," Dettleff said. Because e-commerce retailers capture buying data, they use algorithms to predict what products individuals in certain neighborhoods will likely purchase. "You've got a fleet of vans, typically sprinter vans, just waiting to pull up, get loaded and go off, so you need tons and tons of parking."
It's not just e-commerce vendors using these last mile locations, said Bryden. They are also in demand among "service providers that are supplying the business community [with items like] construction materials and medical supplies."
Dettleff noted that companies like Lowe's, Home Depot and Amazon have their own last mile distribution networks, "but other companies [without their own last mile networks] will probably just send the items to FedEx, UPS or DHL," relying on the last mile networks of those third-party logistics providers.
Locations. Dettleff said that with last mile facilities "it's all about location; how quickly can drivers get to highways to make regional deliveries in neighborhoods?" Bryden concurred saying users of these facilities are "definitely more focused on access to the interstates and truck networks," than they are on ceiling heights or other elements.

Design and circulation. Last mile facilities can range between 50,000 and 200,000 square feet, but the parking requirements are "off the charts" because you need to accommodate hundreds of delivery vans, Dettleff said. He added that tractor trailer access for the site is also a must. He noted that many older facilities built in the 60s and 70s have low ceilings, but they are still usable because at this stage of e-commerce delivery, massive multi-tiered conveyors and shelving are not as necessary as they are in earlier stages. This is because a smaller number of items are processed through these last mile facilities and they tend to arrive then depart in one to three days. "What's really tough about these buildings is that you can't necessarily get tractor trailers into those spaces," Dettleff said.
Bryden noted that these buildings are typically loaded on one side and may have some cross-docking capability. New properties are being built with clear heights of 32 feet; not so much because tenants require this feature currently, but because institutional investors believe those heights will better position properties for the future.
Infill buildings can get much smaller than mid-size structures and range between 75,000 square feet and 200,000 square feet. Bryden noted that some "mimic a traditional flex footprint," coming in below 50,000 square feet.
Bryden added that on many of these sites, developers rarely build as much square-footage as they are allowed per local zoning. "The buildings themselves are fairly simple but our site layout is a critical component of the overall project. Rather than maxing out a site with the largest building possible, considerations for circulation and trailer parking are paramount and elements that we spend a lot of time designing, internally. We could easily shortchange that to get a bigger building, which ultimately increases our overall net profit, but it is a detriment to the asset over time," she said.
Industrial Properties for sale near you
This article was updated on 9/19/2024