How Modern Distribution Centres Need to Adapt to the Needs of E-commerce
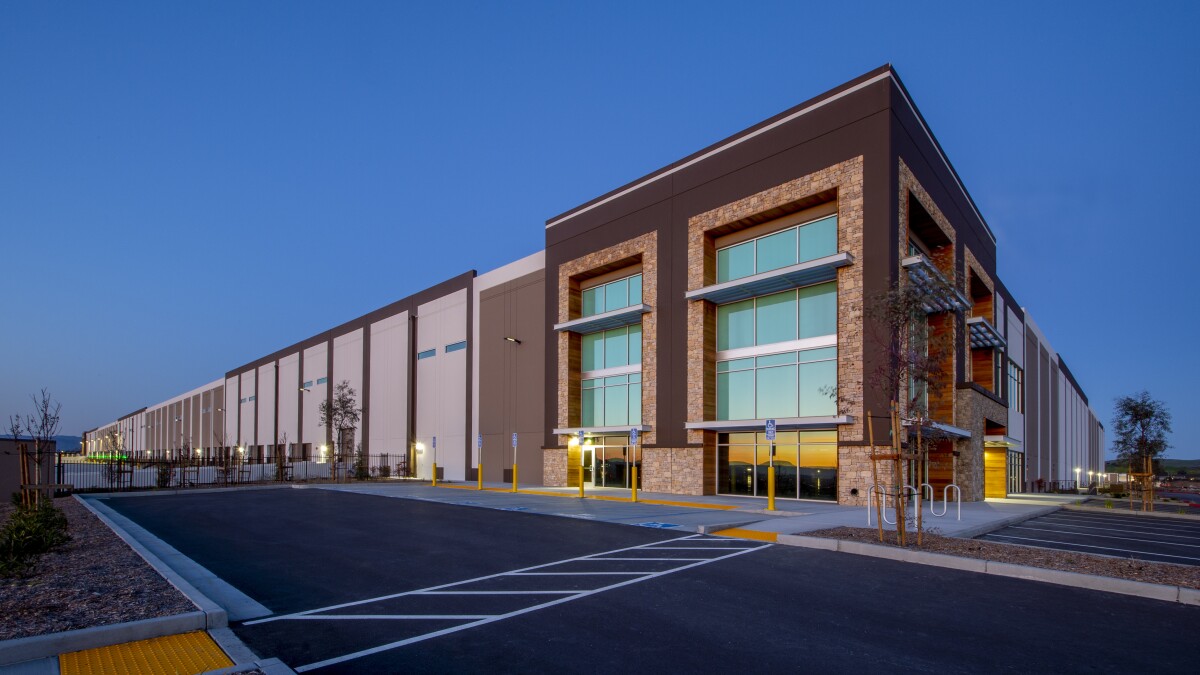
Demand for ‘big box’ retail space is waning as consumers shift toward online shopping, but logistic real estate – warehouses, distribution facilities and fulfilment centres – is on the rise. Given the need for quicker delivery times and lower transportation costs, fulfilment facilities in close proximity to higher-density population centres will be in greater demand and will command higher net rental rates.
However, beyond location, these properties also need to be equipped for the challenge of handling thousands of frequent deliveries of small individual parcels. These may be delivered directly to the consumer from a large distribution centre or via a ‘last mile’ property.
With the shifts in consumer retail patterns in mind, today's e-commerce distribution centres look, feel and operate completely differently than the warehouses of the past. Here's a look at some of the key features a modern warehouse should include in order to accommodate consumers' new shopping habits.
Building size. Online shopping and consumers' demand for swift delivery have pushed the size of e-commerce buildings towards one million square feet or more. Amazon’s ‘mega-shed’ in Tilbury is a four-storey 550,000 sq ft warehouse, with over 2 million sq ft of floorspace. Last-mile facilities located in urban areas are often much smaller, measuring 200,000 sq ft or less.
Don’t waste time and resources finding a warehouse and then outgrowing the space shortly after. Save time and effort by estimating projected growth so you can figure out an accurate idea of the storage your company needs. Flexibility is also key – whether a large distribution centre or a smaller urban warehouse, the building must be able to cope with the demand volatility imposed by e-commerce, as well as trends driven by social media.
Building shape. While a site's configuration and layout will impact building shape, a rectangular shape is ideal for e-commerce distribution facilities with building depths under 300ft for single load design.
Ceiling height. The higher, the better. Most new distribution centres are constructed with 36-ft or 40-ft clearances, but depending on the equipment utilised, some ceilings can be up to 60- to 70-ft-high. Higher ceilings allow for multiple mezzanine decks, thus maximising floor space. As the business grows and volumes increase and capacity becomes paramount, it’s important to take advantage of the full size of the facility – the height, depth and width for the storage of products.
Fire protection. Large storage buildings where more than 7,000m3 (23,000ft3) is used for storing or depositing goods or materials must have Class A fire extinguishers and well-maintained sprinklers – London City Fire Protection recommends ASD (air sampling) smoke detection units for warehouses. These can detect smoke before it’s even visible to the naked eye.
Roofing system. Composite roofing is the most commonly selected roofing and cladding materials for warehouses. It comprises a pre-assembled roofing structure with insulation and support sandwiched between the upper and lower roofing panels.
Warehouse lighting. LED lighting is becoming a standard in all new warehouse construction. BSEUK provide both new installations and upgrades to existing warehouse lighting systems, offering LED fittings with a lifetime of 50,000 hours, along with dimming controls and occupancy detection to reduce lighting costs.
Columns and bay size. The distance between parked trucks should be big enough to open and close the vehicle's doors. Standard loading bays should be at least 3700mm (12ft) although, when accommodating wide trucks with open doors, this should be increased to approximately 4000mm (13ft). Large columns can often limit the goods and stock that will fit in a given space and can affect the flow of materials in and orders going out.
Deliveries. The days when warehouses were serviced only by large articulated lorries are long gone.
Today, there is a wide range of vehicles that warehouses can expect to have to accommodate, and this must be reflected in their design. The rise of e-commerce, and the growth in small, fragmented orders, has driven an increase in the number of small vans making deliveries. Orders that are extremely time-dependent and may even be dispatched individually via motorbikes or scooters. Careful thought must be given to the way in which to best accommodate the increasing variety of vehicles if they are all to be efficiently loaded and unloaded. This may require changes to the layout of an existing warehouse.
Connectivity. Fibre optic broadband for connectivity is now standard.
Technology. Automation systems are present everywhere, from Amazon robots driving entire racks through the warehouse to modern conveyors and multi-level picking systems. The warehouse infrastructure needs to support all this automation and accompanying technology.
People. Large Amazon distribution centres now employ over 1,000 people, so there’s a need for larger amenities such as efficient HVAC (Heating, Ventilation and Air Conditioning) systems, space for breaks and good changing and washroom facilities. These are vital to create a good working environment for staff.
Car parking. Due to the large number of employees now staffed at these facilities, which increases during peak season, having enough parking spaces is very important, along with cycle racks.
Security. Properties must be secured with fencing, gates and dock locks.
Driven by e-commerce, modern distribution centres are becoming bigger, taller and more complex than ever. Developers continue to construct and design space suitable for these types of occupiers, with much of the inventory pre-leased in advance.
Users will look to find space that can handle the increasing demand on shipping, logistics, delivery, and returns. Once they've optimised for location, demand, labour pool, and transportation costs, they'll look to maximise efficiencies within the layouts and buildings themselves.
This article was written by Goran Brelih, senior vice president of Cushman & Wakefield ULC in the Greater Toronto Area, and originally publshed on Realla on 19 July 2019.